Sheet Metal Stamping
Sheet metal stamping is used to transform flat metal sheets in specific shapes.Stamping of sheet metal is a process based on permanent deformation by cold forming to produce a variety of complex three-dimensional shapes.
Tensile forces with high ratio of surface area carry out the process to thickness. The stamping of sheet metals is very common: this is the reason why many objects in your house are the result of a metal stamping process.
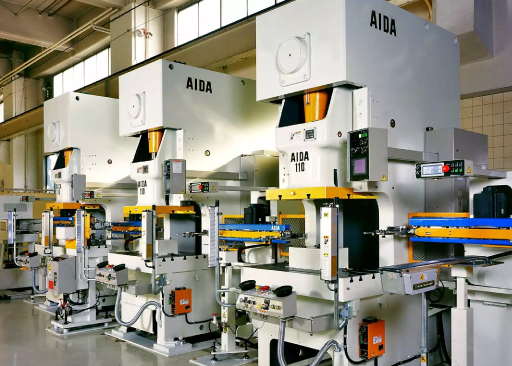

Vacuum Transfer Moulding
Transfer molding is a manufacturing process where casting material is forced into a mold. Transfer molding is different from compression molding in that the mold is enclosed [Hayward] rather than open to the fill plunger resulting in higher dimensional tolerances and less environmental impact. Compared to injection molding, transfer molding uses higher pressures to uniformly fill the mold cavity. This allows thicker reinforcing fiber matrices to be more completely saturated by resin. Furthermore, unlike injection molding the transfer mold casting material may start the process as a solid. This can reduce equipment costs and time dependency. The transfer process may have a slower fill rate than an equivalent injection molding processes.
Compression Moulding
Compression Moulding is a method of moulding in which the moulding material, generally preheated, is first placed in an open, heated mould cavity. The mould is closed with a top force or plug member, pressure is applied to force the material into contact with all mould areas, while heat and pressure are maintained until the moulding material has cured. The process employs thermosetting resins in a partially cured stage, either in the form of granules, putty-like masses, or preforms.

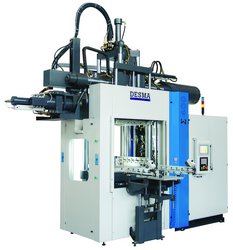
Rubber Injection Moulding
The rubber injection molding process starts with an uncured rubber ribbon stock that is fed into a rotating screw of the injection unit. A controlled amount of material is pulled into the injection unit. Here the material is plasticized to a target elevated temperature. The rubber material is then injected into the mold cavity through a runner and gate system where it is held in the mold under high pressure and elevated temperature to activate the cure system in the rubber compound (rubber is vulcanized). The cycle time is established to reach an optimal level of cure. At the end of the cycle, the parts are removed or ejected from the cavities and the next cycle begins.
Plastic Injection Moulding
Plastic injection moulding is the process of melting plastic pellets (thermosetting/ thermoplastic polymers) that once malleable enough, are injected at pressure into a mould cavity, which fills and solidifies to produce the final product.
The thermoplastic injection moulding process at Protolabs is a standard process involving an aluminium mould. Aluminium transfers heat much more efficiently than steel, so does not require cooling channels – which means the time we save on cooling can be applied to monitoring fill pressure, cosmetic concerns and producing a quality part.
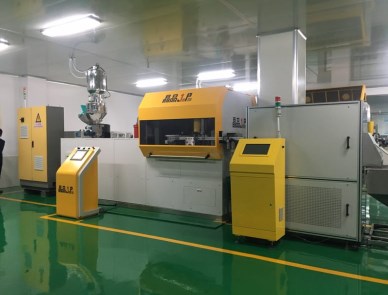