Verticle Machining Center (VMC)
CNC vertical machining centers (VMCs) remain machine shop staples. These milling machines have vertically oriented spindles that approach workpieces mounted on their table from above and commonly perform 2.5- or 3-axis machining operations. They are less costly than horizontal machining centers (HMCs), which makes them attractive to small job shops as well as larger machining operations. In addition, the performance of these machines has increased over the years, leveraging technologies such as high-speed spindles and advanced CNC capabilities (including conversational control programming). Ancillary equipment is also available to increase the flexibility and capability of these machines, including spindle speeders, angle heads, tool- and part-probes, quick-change workholding devices, and rotary indexers to enable four- or five-axis machining work.
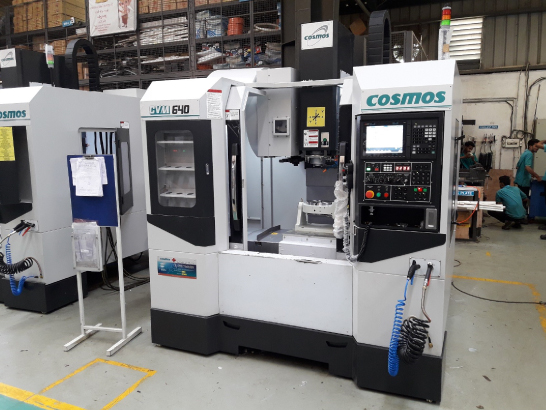
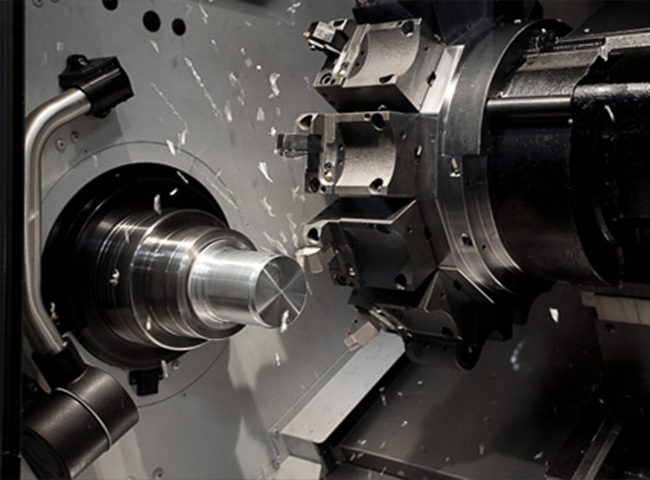
CNC Turning Center
Through modern computer technology and skilled operators, a component can now be created to the minutest detail and to the most rigid of designs using a Turning Lathe, with precise tolerances and a vast array of shapes. The turning lathe secures and rotates the stock, or raw material, being machined along a dual axis of movement at high speeds, while a single point cutting or boring tool shapes the material, resulting in the desired component being created. The lathe is controlled by computer programs; ensuring meticulously exact components are produced, and can also be reproduced. At MNB, we pride ourselves on being experts in the latest CNC Turning Technology and Processes, and on our ability to create the components our customers demand swiftly, efficiently and precisely.
Wire Cut EDM
Wire electrical discharge machining (EDM) is a process of metal machining in which a tool discharges thousands of sparks to a metal workpiece. A non-conventional process, wire EDM works on parts resistant to conventional machining processes, but only if these parts are electrically conductive; usually, they are non-ferrous, and include steel, titanium, super alloys, brass, and many other metals. Instead of cutting the material, EDM melts or vaporizes it, leaving little debris and providing a very accurate line. Industry-wide acceptance has led to a wide variety of EDM applications, as it is highly versatile, can cut hard metals, and utilizes a relatively compact amount of workspace.
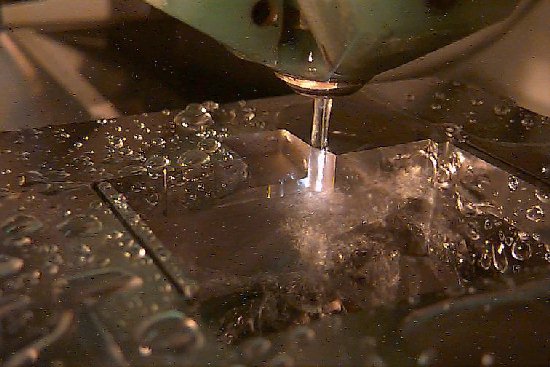
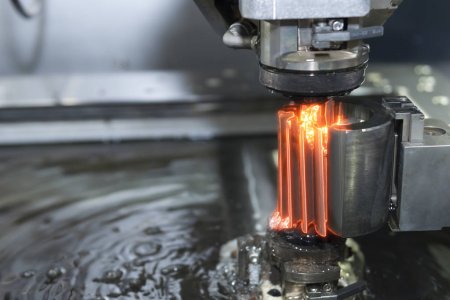
Electric Discharge Machine (EDM)
When traditional machining methods reach their limit, electric discharge machining can be the answer. The EDM process allows for high accuracy and is applicable for any conductive material.
Electrical discharge machining, or EDM, is a non-traditional method in which material is removed from a workpiece using thermal energy. Much like processes such as laser cutting, EDM does not need mechanical force in the removal process. This is the reason why it is considered non-traditional contrary to, for example, the processing with cutting tools.
In tool and mould making, EDM is very popular due to its applicability especially for hard materials like titanium or for particularly complex shapes that are hard to achieve with milling.